Tilt-up or tilt-wall construction consists of reinforced concrete walls that are poured horizontally on-site and lifted (tilted) into place when sufficient strength has been attained. The walls are site cast on the building slab or on casting slabs with all openings, embeds, recesses, formliners and even facades such as thin-brick. It can be a time-saving and cost-effective method of construction making it a popular choice for all building sectors.
There are many benefits to utilizing tilt-up construction including schedule, aesthetics, fire resistance and durability. Tilt-up construction is relatively quick to cast and erect making it a desirable form of construction when schedule is a high priority. Various formliners and finishes such as thin brick and integral color can be incorporated to provide an aesthetically pleasing finished product with limited labor required after the panels have been erected.
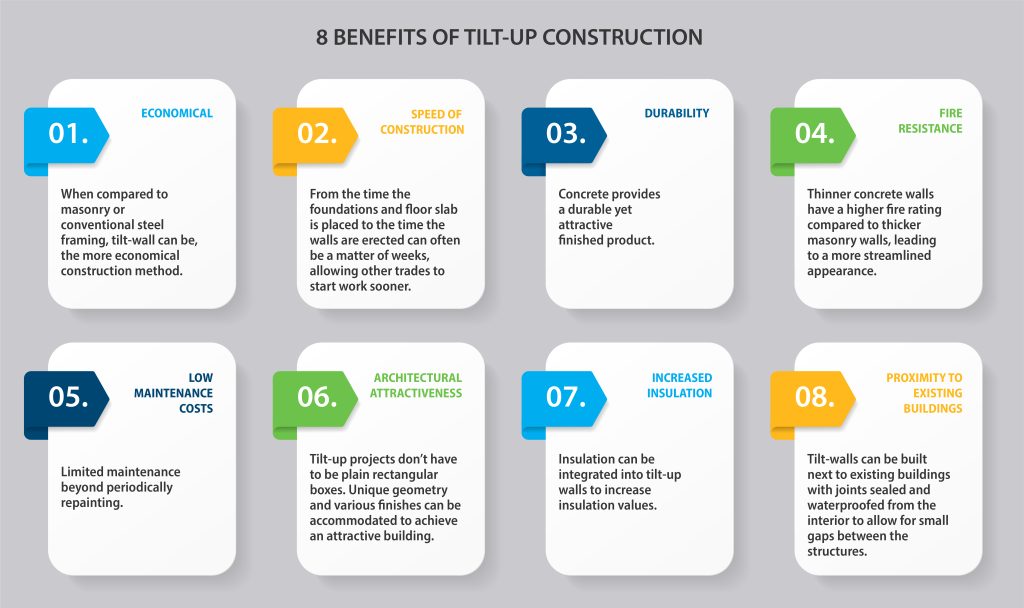
There are several elements that create ideal conditions for a tilt-up project in terms of being the most economical solution. These include the size of the building, location of the building, importance of schedule, panelization geometry, and casting slab. Even if some of the ideal conditions are not met on a project, tilt-up construction may still be the preferred solution.
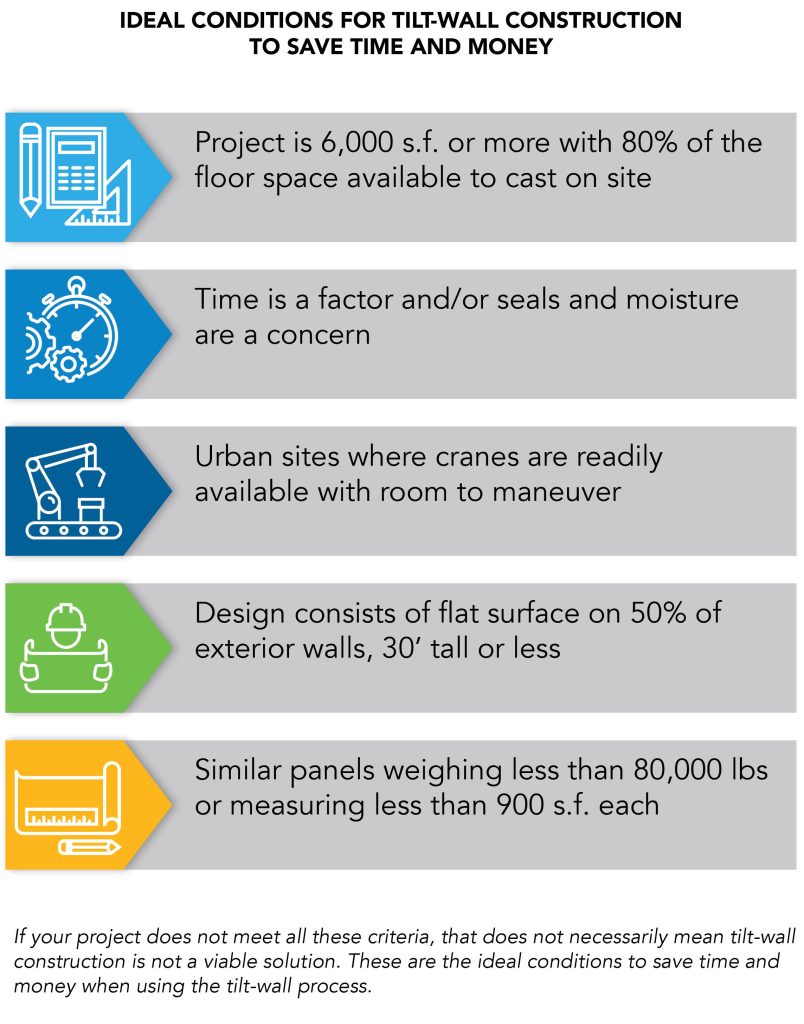
Large panels weighing more than 80,000 pounds are sometimes required when tall, unbraced panels must use thicker panels or when accommodating architectural considerations. This results in a larger than average crane required to lift the panel into place, which comes with a higher cost. The added cost of the larger crane can be counteracted by saving time for lifting by increasing the average panel size. One large panel takes the same amount of time to lift and place as a smaller panel. Projects with limited casting area and tight construction sites can utilize stack casting where similar panels are cast one on top of the other to save space. This requires careful planning by the contractor to sequence the panel pours and lifting order. In extreme cases, the location of the crane may be carefully coordinated with the stacked panels and order of lifting so that as panels are erected, more space is available for the crane.
A unique project where conditions weren’t 100% ideal for tilt-wall, but it was determined to be the right fit for the project, is the City of Winter Haven AdventHealth Field House and Conference Center. (Please click the project name to learn more about this expansion of an existing building.) The panels are set one inch from the existing building and was the 2019, Ridge Chapter, Florida Engineering Society Project of the Year.
Feature Project: Cocoa Beach Police Headquarters
The City of Cocoa Beach Police Headquarters in the heart of downtown Cocoa Beach on the east coast of Florida is a project where not every ideal condition applied and yet tilt-up was still the preferred solution. The project met the conditions for size, accelerated schedule, and fire resistance. However, the building is a tall three-story building located in the downtown area and is surrounded by roads and buildings.
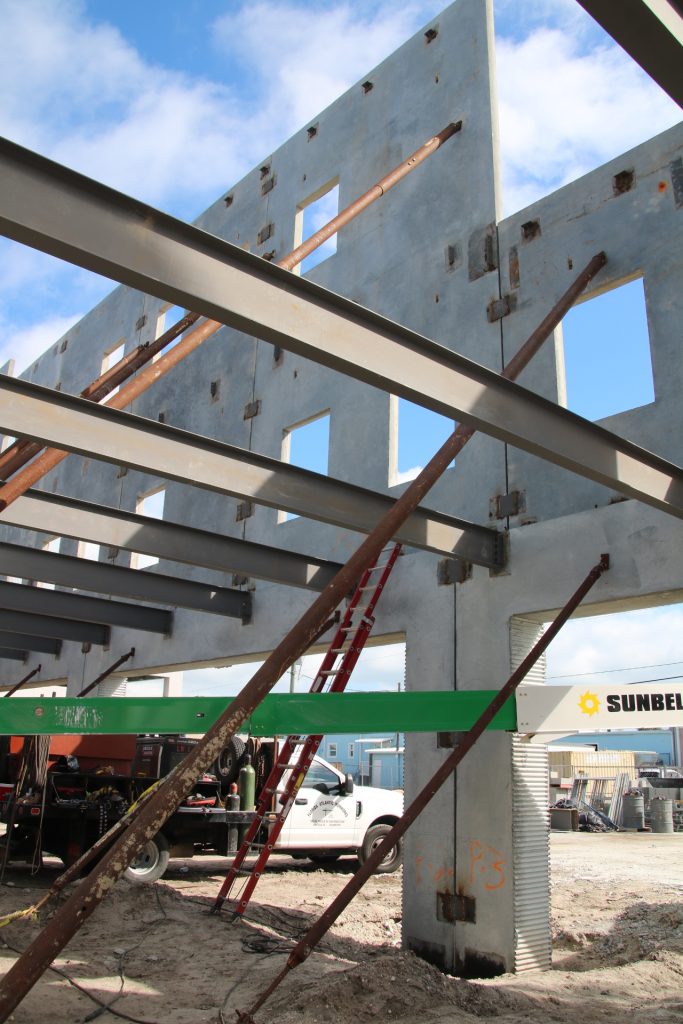
There was limited space available on site for casting the panels and for the operation of the crane during lifting. The building slab was too small to cast the large panels side by side and no space was available for casting slabs. An alternative option to site-cast tilt-up walls is precast walls that are fabricated off-site and transported to the site. Precast walls were eliminated due to the height of the panels being almost 50 feet combined with the path of travel required to get to the site requiring tight turns and shutting down traffic during transportation. Transporting panels is an added cost to precast and the logistics of transporting large panels can be complicated. The solution was to stack cast the panels which took coordinated effort between the design team and the contractors.
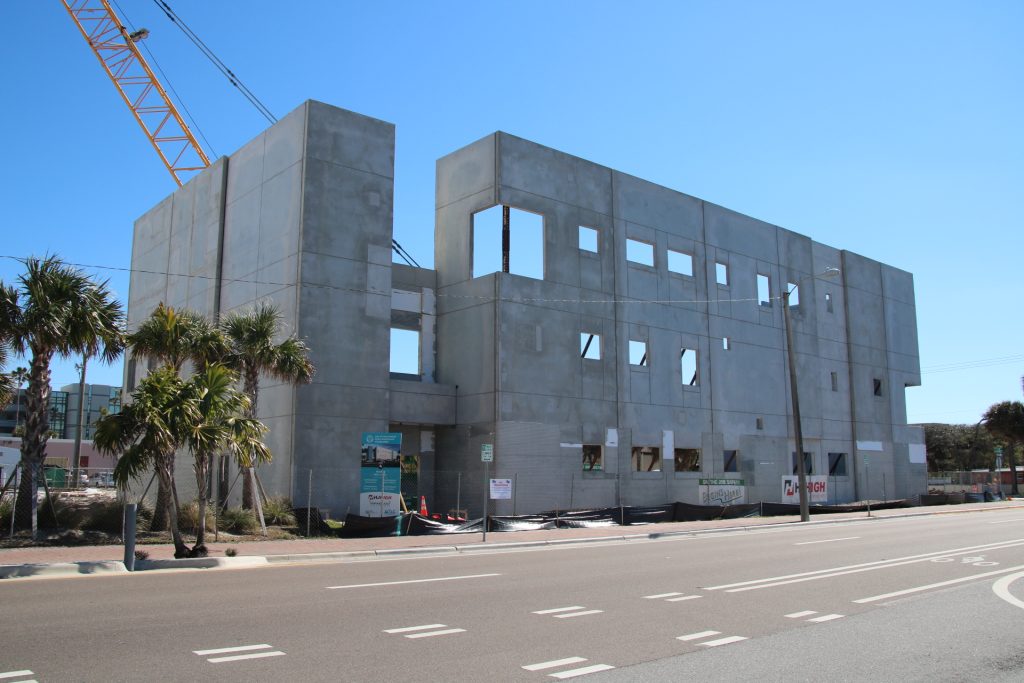
The design team economized the panels by creating as many similarly sized panels as possible allowing for the panels to be stacked together. The general contractor, H.J. High Construction Company, and the tilt wall subcontractor, VMG Construction Inc., created a plan detailing the order for casting the panels and the exact location on site for each panel. This was coordinated with the movement of the crane and the lifting order of the panels. The crane essentially had to back out of the building as panels were lifted. Please watch video 1 to appreciate the choreography that takes place and video 2 to see the impressive final results. Click City of Cocoa Beach Police Headquarters to discover other aspects of this project and images of its completion.
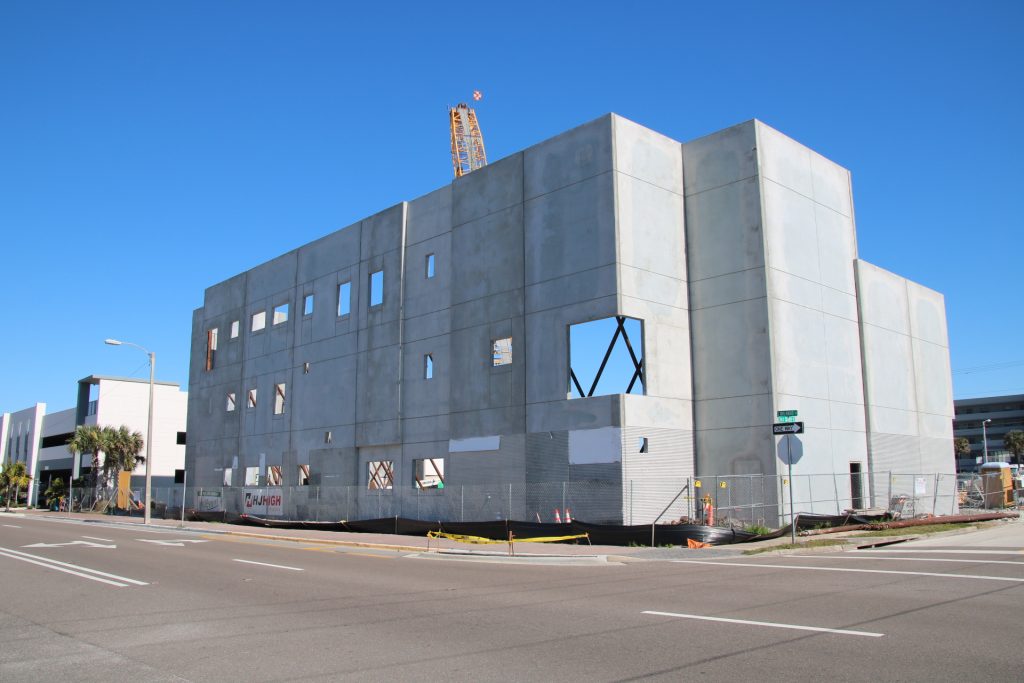
It’s clear that tilt-up or tilt-wall construction can be a time-saving and cost-effective method of construction and can be a solution for a multitude of challenges in a many different situations. To explore more TLC structural projects or to discuss if tilt-up construction is right for your project, please contact one of our structural experts. (Click here.)